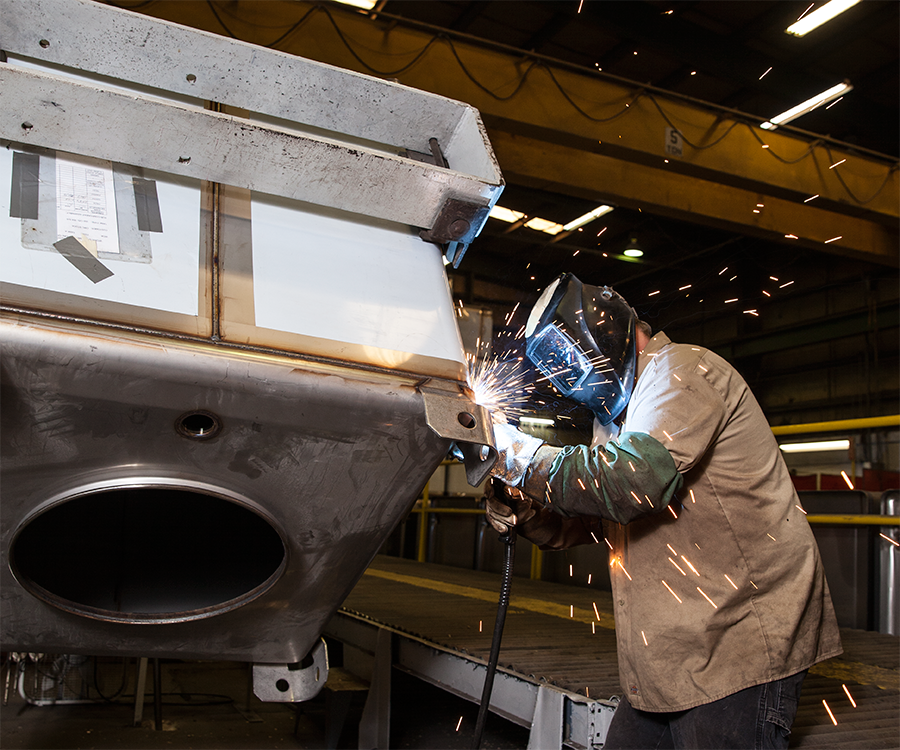
Strategy
A Steel Foundation
Stop before you sip. Some of your favorite libations, liquids and liquors have one thing in common: stainless steel tanks. Follow the journey one manufacturing company’s product takes to tie together some of Springfield’s biggest industries.
By Claire Porter | Photo By Brandon Alms
Mar 2016
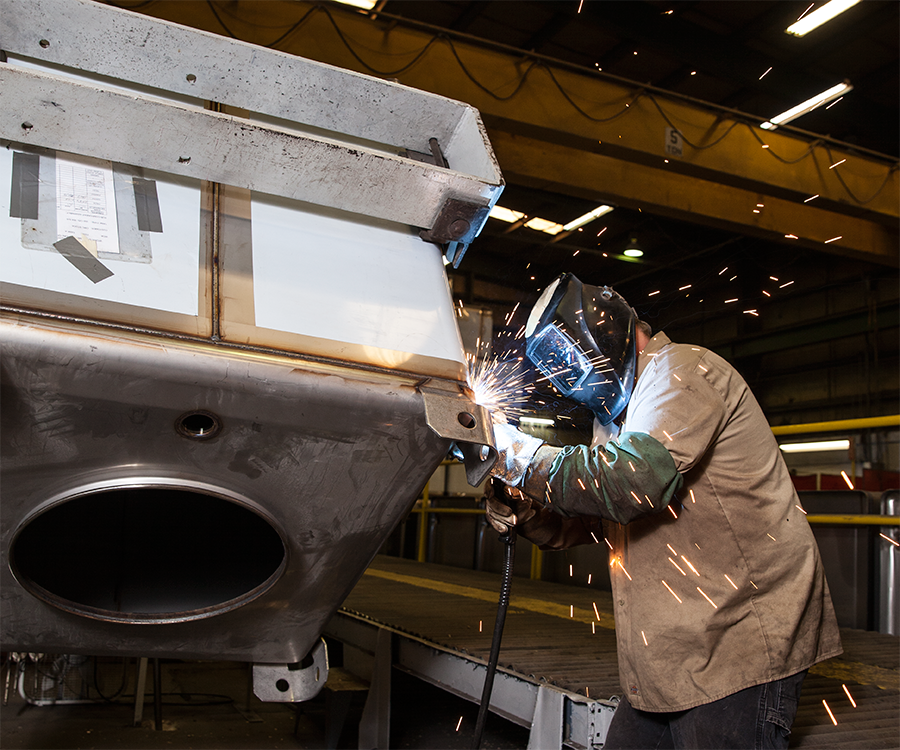
As the elevator doors slide open with a ding and you step into the warm glow of Barley Wheat & Rye Social House, you’re greeted with a wall of whiskeys and bourbons. Peeking out among bottles from enough countries to fill a passport is a brew that’s closer to home, J. Rieger’s “KC Whiskey.” As you swirl your glass and sip, you might be thinking about the Missouri-based craftsmen behind your brew, but every inch of your unwinding experience was brought to you by workers—most of them local—in industries far removed from whiskey. From the paints that drench the walls and adhesives holding down the carpet under your feet to the cleaners that keep the bar top gleaming, almost every part of an evening out—whiskey included—have one thing in common: They all start with a stainless steel tank.
Custom Creations
Locally, Custom Metalcraft is one of the biggest names behind the stainless steel tank industry. Custom Metalcraft was founded in 1977 by Dwayne Holden and Jerry Cowen, and the company has stayed in Springfield ever since. As the name implies, Custom Metalcraft creates custom stainless steel processing equipment and storage units and handles every step of the process from design to manufacture. The company headquarters employs 170 (not including its licensees in places as far-reaching as Australia). The TranStore Division facility, which is responsible for actually manufacturing each tank sold, employs 55, each of whom helps build the products by hand.
Manufacturing jobs such as these make up the fifth largest employment sector in Springfield and have seen strong and steady growth. Manufacturing employs almost 15,000 people in Springfield alone. According to Scott Higgins, manager of Custom Metalcraft’s TranStore Division, Springfield is an attractive place for manufacturing jobs because of the great work ethic of 417-landers who are highly trained thanks to education programs catered to the specific needs of local companies. Higgins cites the welding programs available at Ozarks Technical Community College and the Midwest Technical Institute for churning out highly skilled local employees who are able and more than eager to fill the exacting specifications his facility requires.
Companies like Custom Metalcraft impact industries beyond the education and manufacturing arenas supplying their workers. Any business, company or industry that uses storage tanks, processing equipment or mixing drums could count itself among Custom Metalcraft’s clientele. Those businesses range from pharmaceutical processing and petroleum drilling mega-companies to paint shops and small-batch distilleries or breweries. But before these businesses can get their products flowing, the tanks have to reach them first.
The Road to Profits
Higgins points out that Springfield’s location makes it prime for production and manufacturing companies because of its easy access to highways, railways and waterways. “Because we’re in the middle of the U.S., our shipping is very competitive,” he says, compared to shipping from the coast where getting materials and products across the country takes twice as long and costs even more.
All of that is good news for the local economy. In 2014, the Springfield Metro Area exported more than $450 million, with electrical equipment and appliance and component manufacturing products making up almost a third of those exports, according to the Missouri Economic Research and Information Center.
One of the largest and most accessible ways for companies like Custom Metalcraft to ship out of 417-land is by truck, thanks to the convenient locations of Interstate 44, Highway 65 and Highway 60. Custom Metalcraft uses major national companies such as SAIA, FedEx and UPS, which can cover a lot of ground. For industries outside of Custom Metalcraft, local trucking companies such as Prime, Inc. can compete with the big players just as well.
Although trucking is the most efficient method of exporting goods, it requires a few extra steps. Because of Custom Metalcraft’s high volume—the TranStore facility produces 7,500 tanks each year—the team has perfected the licensing procedure necessary for packing their products on trucks. The Department of Transportation requires that each tank has its own license plate of sorts, which means a lot of paperwork, and a lot of back and forth with some of the 28,800 government employees in the Springfield Metro Area. Once each tank is labeled and ready to go, it's loaded onto a truck and headed to customers near and far.
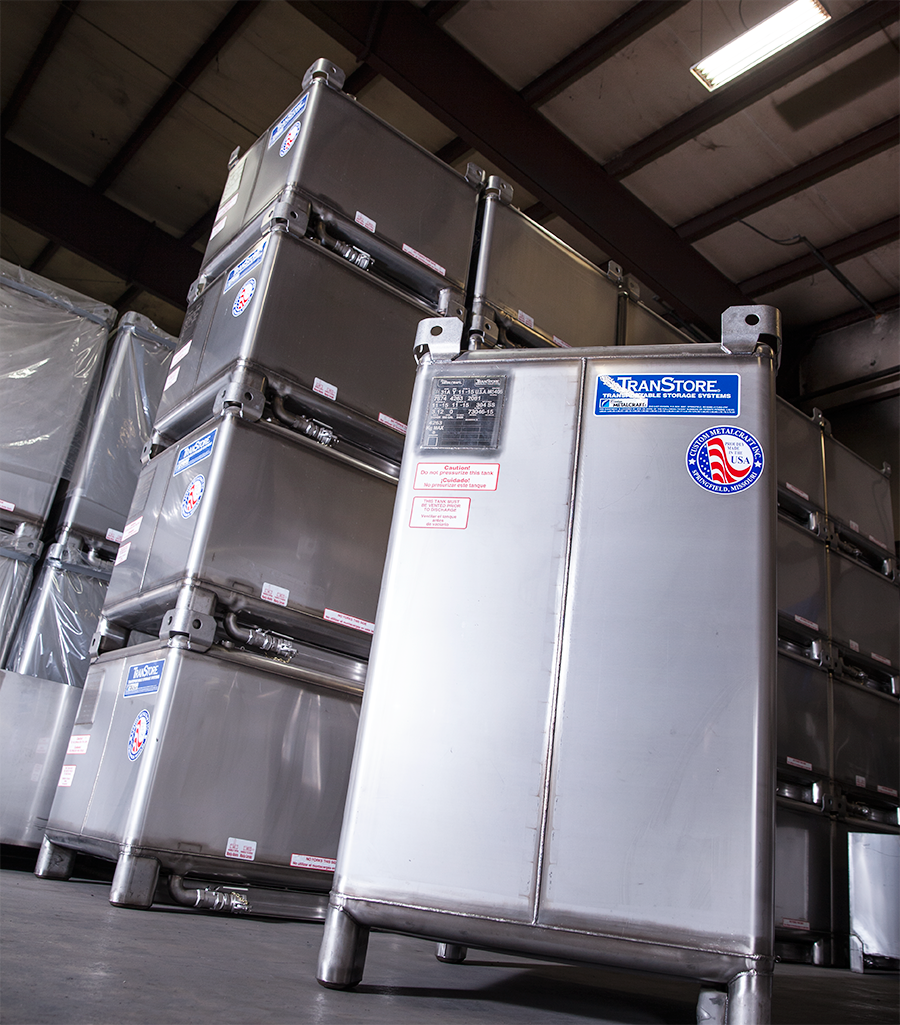
A finished standard Custom Metalcraft tank stands four feet tall and can hold 350 gallons. The square shape allows tanks to be stacked four tanks high without creating wasted space between them.
In the Neighborhood
Some road trips don’t take very long. For a hyper-local look at the tanks in action, peek outside the liquor industry and into the world of chemicals. To deliver a shipment of tanks from the TranStore facility to Superior Solvents & Chemicals takes a mere 20 minutes heading west on Chestnut Expressway. There, the tanks serve a more industrial purpose.
Superior Solvents & Chemicals is a division of Superior Oil companies, which is a nationwide independent chemical supplier and fiberglass distributor. In its 20-person Springfield facility, the operations team produces a variety of oil-based chemicals, fiberglass and resins. For these uses, Custom Metalcraft workers put specific coatings on the tanks to protect the stainless steel and spend extra time sanding and smoothing the interiors to prevent chemical residue and dangerous mixing. Through various blending, mixing and repackaging processes, solvents and chemicals pass through several Custom Metalcraft tanks, funnels, scrubbers, dumpers and conveyors to turn into solvents used in everything from automobiles to shampoos in facilities across the nation.
Down a Dram
Although other trips are longer, sometimes the fruits of those journeys land closer to home. Custom Metalcraft also ships tanks to the J. Rieger & Co. distillery. This Kansas City brand was founded in 1887, but went out of business during Prohibition. Now, owner Andy Rieger is back in business with help from stainless steel mills, fermenters, cookers and distillers he uses to make the brand’s signature whiskey. Unlike wood and copper elements used in traditional whiskey-making, the stainless steel of Custom Metalcraft products lasts longer, withstands more wear and can be cleaned, reused and recycled, making it a sound investment for a cost-conscious business.
The distillery produces about 5,000 bottles of whiskey per month, which are then picked up by distributors and shipped back out to restaurants, bars and liquor stores. Although the distillery is run by four Kansas Citians, J. Rieger & Co.’s products help keep the bar shelves stocked at several of Springfield’s 591 licensed restaurants and bars.
It’s easy to identify the work of craftsmen like Rieger when savoring a glass of whiskey, but his artistry wouldn’t be possible without an entire community of businesses and industries working in tandem. Rieger wouldn’t be able to bottle a 92-proof perfectly aged whiskey without the infrastructure provided by Custom Metalcraft. Custom Metalcraft wouldn’t be able to make those tanks without the skills and dedication of trained and educated welders and workers, and none of them would be able to ship the products without a team of certified truckers and drivers delivering local goods to businesses near and far. So, next time you head out, raise a glass to all of those who made filling it possible.
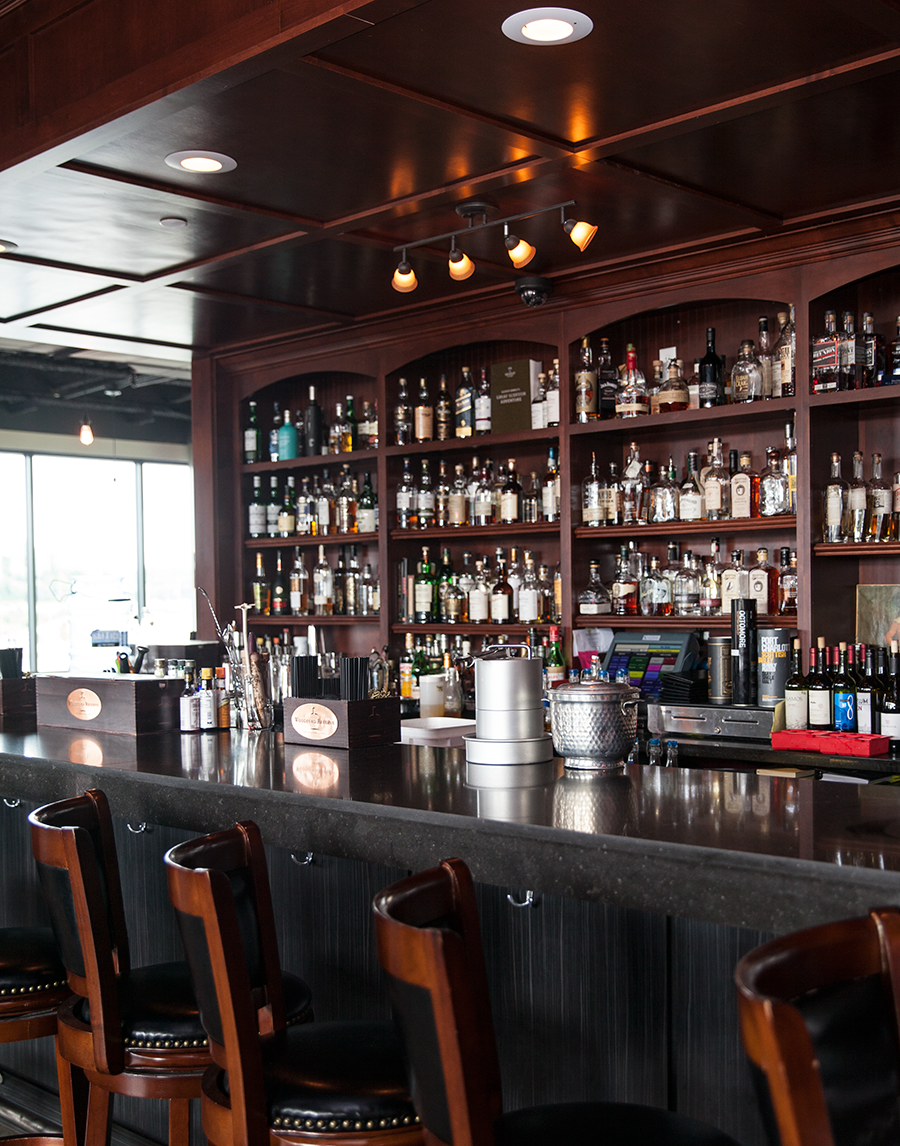
J. Rieger & Co.'s whiskey originates in Kansas City, but the components that make it possible start in 417-land and end up in places like Barley Wheat & Rye.
Ride Along
Follow the path that meanders through 417-land (and beyond!) and makes up a lifetime for a Custom Metalcraft stainless steel tank.
Square Beginnings
The journey begins with a square stainless steel sheet at a factory in Mount Vernon. The specifications of a tank depend on the customer’s order, but standard ones are 350 gallons and almost four feet tall. Once an order is placed, the sheets are shipped to Custom Metalcraft's Springfield facility.
Hand-Hewn Hardware
Steel tops and bottoms, or sub-parts, are made first. Then, workers along an assembly line bend sheets around the sub-parts and weld them in place. All seams are sealed, sanded and smoothed. To cap off the 8-hour assembly, each tank is either washed by hand or put through a sanitizing wash.
License to Fill
Empty tanks bound for oil or petroleum companies require special licensing to be transported across state lines. Once registered, they’re loaded onto trucks for delivery. A Custom Metalcraft tank's advantage is its shape. The rectangular tanks can be stacked four high and eliminate wasted space.
Brimming Bottles
Some tanks end up at J. Rieger & Co., whose whiskey depends on Custom Metalcraft’s tanks. Grains start in a grain mill and then are put into a mash tun with hot water. The mixture is fermented and distilled before going into American oak barrels for several years. Once aged, the whiskey is sent through another stainless steel tank to be bottled. The finished product is then labeled and ready for sale.
The Local Loop
The cycle ends in 417-land when distributors pick up the bottles and deliver them to local restaurants, bars and shops such as Barley Wheat & Rye Social House, Macadoodles or Brown Derby International Wine Center.